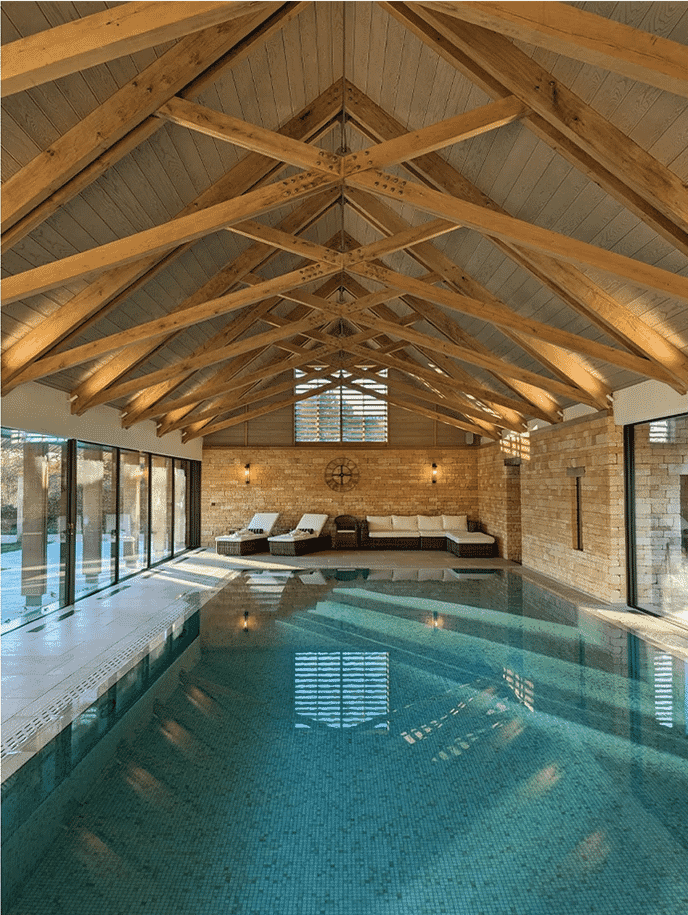
A guide to glazing for swimming pools
The key considerations for choosing glazing for swimming pool environments
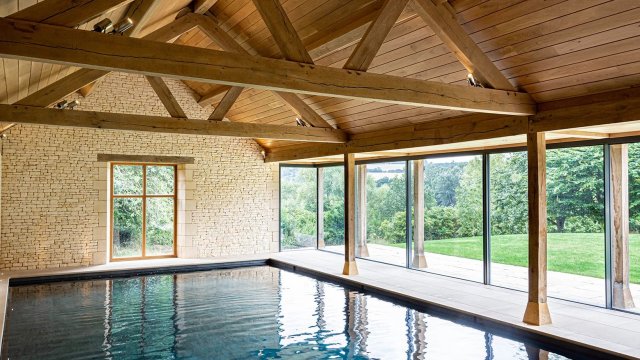
Glazing for swimming pools, whether indoor or outdoor, presents a unique set of challenges. Poolside spaces are subject to high humidity, fluctuating temperatures, chemical exposure, and condensation.
To ensure performance and longevity, glazing systems in these environments must be carefully specified – not only in terms of aesthetics and thermal performance, but also with regard to corrosion resistance, glass safety, and durability. At Cotswold Windows, we work with leading-edge glazing systems such as Sky-Frame and MHB steel windows and doors, both of which offer advanced solutions specifically suited to pool environments. This private pool house with bespoke glazing in Broadway in the Cotswolds is an example of how swimming pool glazing can be both design-led and performance-related. In this article, we’ll explore the critical factors to consider when designing and specifying glazing for pools, whether residential or commercial.
Glazing considerations for poolside dwellings
1. Surface treatments for harsh environments
Swimming pool environments are highly corrosive. The constant presence of moisture, and in many cases chlorine or saline chemicals, means that standard surface finishes on aluminium or steel frames are simply not sufficient. For all our swimming pool glazing, our products have the following treatments:
Aluminium: powder coating and anodising
As a surface treatment, powder coating acts as a protection to stop the aluminium oxidising. For aluminium systems such as Sky-Frame, the powder coating must comply with Qualicoat Class 2, an internationally recognised standard for coatings in aggressive environments, including pools and coastal locations. Class 2 coatings offer higher resistance to UV, humidity and chemical exposure than standard Class 1 finishes.
Anodising is another highly effective treatment, offering excellent protection by altering the surface chemistry of the aluminium itself. Unlike powder coating, which is applied over the surface, anodising creates a deep, integrated layer of protection within the metal. In particularly demanding projects, some clients opt for a dual finish: anodising followed by powder coating for maximum durability.
Steel: multi-layered protection and welding
Steel systems require a different approach as they are more prone to corrosion in poolside and marine environments. Following the international Qualisteelcoat standard, MHB Steel uses a surface protection hierarchy based on environmental exposure – C5 is the highest level of surface treatment and protection from corrosion you can get for pools and marine environments, involving multiple layers of zinc-rich primers and a powder-coated or anodic topcoat.
MHB also offers laser welding for all frame joints, creating a seamless, fully sealed weld that eliminates crevices where moisture might accumulate. This technique also prevents internal corrosion, which can cause problems and be a critical issue when using folded sheet hollow-section steel systems. Unlike some other steel framed systems, MHB frames are constructed from solid steel profiles, giving it another advantage in poolside settings. You can find out more about the differences between MHB and other steel frames in our recent blog.
2. Glass specification for swimming pools
Poolside glazing should always be specified with the environment in mind – not only in terms of visibility and light transmission, but more importantly for safety and durability.
Laminated vs toughened glass
Glass located within two metres of the pool edge should always be laminated, not toughened. While toughened glass shatters into small fragments on impact, laminated glass maintains its structural integrity, even when cracked. This is particularly important in wet, barefoot environments where the risk of injury must be minimised.
At Cotswold Windows, we recommend laminated glass as standard for all pool installations, not just where required by regulation. Both Sky-Frame and MHB systems can be specified with laminated glazing options to ensure compliance and safety.
Glazing units and sealants
Due to the high humidity levels found around pools, triple glazing is often recommended to reduce the risk of internal condensation. You can find out more about What causes condensation and how to prevent it in our blog.
In these environments, special attention is also paid to the sealant used within the glazing units. We specify sealants designed for exposure to chlorine or saline-rich air, to maintain integrity over time.
If there is a lot of glass, then an air management systems will often be used – for instance, to control condensation through air curtains or mechanical ventilation. Glazing can be fitted with electrical position monitoring systems which integrate with building management systems to automate ventilation.
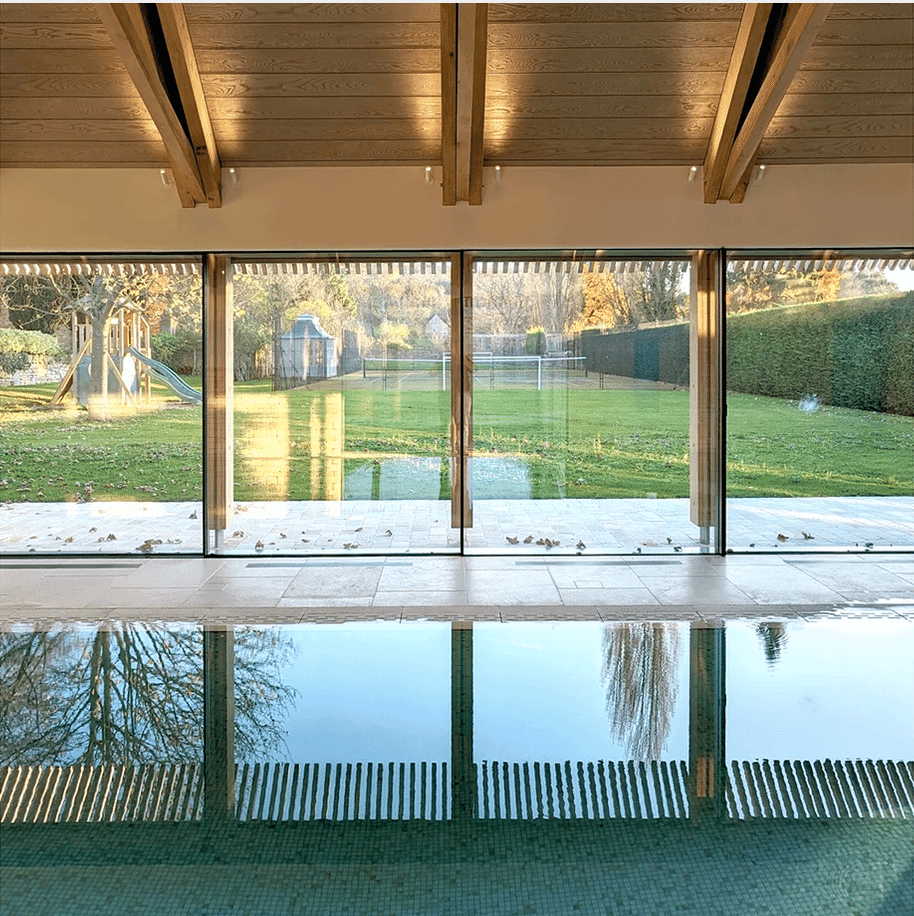
3. Innovative design and accessibility
Glazing for swimming pool environments should offer not only durability but also user-friendly design. The Sky-Frame Plain system is particularly well-suited to this purpose. It allows floor tiles to run continuously from the pool edge across the door track, creating a perfectly flush finish from poolside to garden or terrace. This is not only visually stunning, but also safer and more comfortable for bare feet – avoiding the need to step over exposed aluminium tracks. The system’s concealed drainage and invisible framing create a minimal aesthetic with an absolutely seamless transition between indoor and outdoor. For more design-led projects, take a look at the bespoke glass extension we created for an indoor pool and gym at this country home in Shipton.
4. Hardware and finishing touches
Ironmongery and hardware used around pools must be equally resistant to corrosion. We specify stainless steel components, which can be powder-coated to match the rest of the frame system if required. Hinges, handles and fixings are all selected for their ability to withstand high humidity without degrading over time.
Position sensors, integrated with pool air control systems, can also be included to ensure environmental systems operate efficiently in tandem with glazing usage.
5. Design and specification support
Whether you’re designing a private indoor pool for a country house, like this contemporary pool pavilion for a Grade II listed manor house that we specified in Minchinhampton, Gloucestershire, or specifying glazing for a coastal property, as we did for this sea-facing property in St Austell, Cornwall, the key is early-stage planning and attention to detail. Selecting systems like Sky-Frame and MHB ensures access to the latest in precision engineering, tested surface protection, and detailing.
At Cotswold Windows, we offer detailed technical support at every stage of the design process. From advising on appropriate surface treatments to ensuring that threshold levels, glazing safety and environmental integration are fully resolved, we work closely with architects, contractors and homeowners to deliver tailored glazing packages suited to even the most demanding environments.
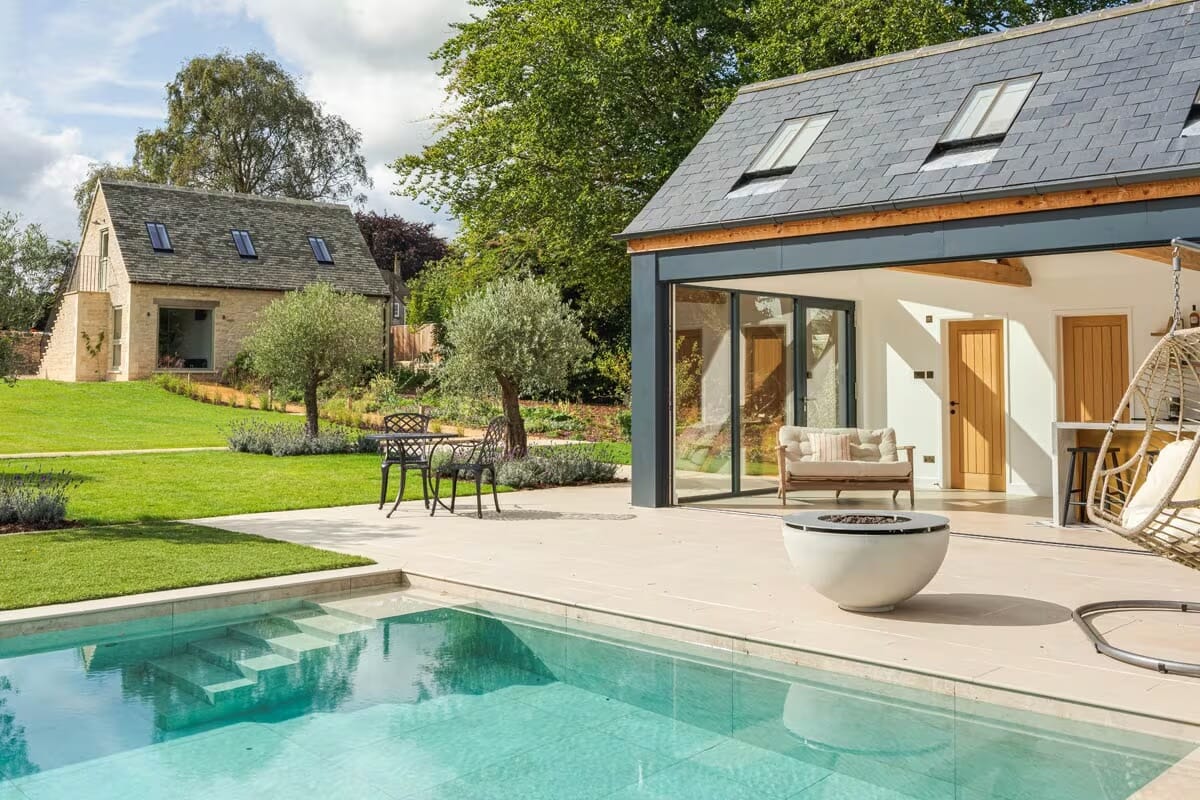
Choose the right glass for your swimming pool project
With the right specification, glazing can enhance the luxury and performance of a pool environment, but getting it wrong can lead to premature failure and costly maintenance. By working with proven systems such as Sky-Frame and MHB, and engaging a specialist glazing partner like Cotswold Windows, it’s possible to achieve a beautiful, functional and long-lasting result. Contact our team for advice about your swimming pool glazing project.